
Faraz Iqbal | Mechanical Engineer
Manufacturing Process Improvement
Saint-Gobain: Norton Abrasives

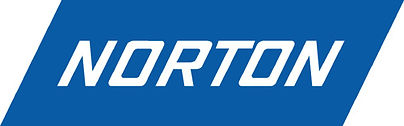
Norton, bought by Saint Gobain in the 1990s, is one of the largest producers of grinding wheels. The superabrasives department is looking to speed up and improve the operation by which diamond is applied to their blades, as this is the bottleneck in their current manufacturing process. Diamond application is currently done manually by a single operator, and when the company receives large orders, the operator has to work overtime to meet deadlines. The student team started by breaking down the operation into individual steps and recording how long each step takes. The ultimate goal is to identify steps that can be eliminated or improved by designing new fixtures and tools as well as possibly rearranging the manufacturing cell layout. Since most of the specifics are considered to be proprietary information, the details of the solution cannot be shared, and images of the process being done cannot be publicly displayed. However, the team has successfully suggested improvements that would allow for a decrease in cycle time by 30% as well as quality improvement of the diamond coated region on the blades. Furthermore, these improvements are very cheap and would save the company a fair amount of money if implemented.
This project was done as a capstone project, a graduation requirement for engineering students at Boston University. On May 3rd, 2018, the team gave a pre-approved presentation to the College of Engineering which was also recorded and can be viewed here. This was my first experience with manufacturing engineering, and I thoroughly enjoyed it. Being able to confidently say that my work on this project could leave an impact on such a large company if the proposed concepts are implemented is awe-inspiring, and I am genuinely proud that the team's efforts produced real results.