
Faraz Iqbal | Mechanical Engineer
Automated Imaging of Microtiter Plate

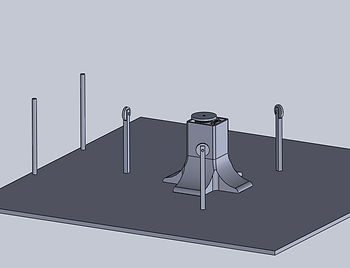
An automated imaging system is to be designed for taking pictures of individual wells in a 3”x 5” transparent microtiter plate (used in the pharmaceutical industry for mixing chemicals). The imaging system has to be able to automatically handle a stack of 50 plates with 24 wells, and the imaging of a single plate has to be completed within one minute. In this project, handling is defined to be loading of the plates into the imager, imaging the individual wells, and then outputting the plates. The team has proposed a design that involves the user loading three plate holders with a capacity of 18 microtiter plates and setting them on a table with a three-axis robotic arm that sits on a linear drive. The robotic arm takes a plate holder and places it onto a turntable that is operated by a stepper motor. The turntable spins the plate holder into the imager, which has a camera mounted on a gantry system similar to that of a 3D printer. While imaging is occurring, the robotic arm will pick up the next plate holder and place it on the turntable. After imaging is complete, the turntable spins, which inputs the new plate holder, allowing the robotic arm to take the completed plate holder back to its original place and putting down a third plate holder. If this design were to be implemented, the system would also allow for varying amounts of microtiter plates which the user would be able to input into the system.
This project was completed during my senior year at Boston University as part of a machine design course. It was by far the most complex project I have worked on, as it involved complete automation to allow for ease of use for the client. Due to the project complexity, meeting deadlines was very difficult. The biggest takeaway from this project for myself as well as my team members was learning how to efficiently divide tasks such that each team member's strengths were utilized in helping meet the time constraints. It is also important to note that this project has a lot of potential for future improvements, and had the group been given a full year to work on this project rather than three months, the final product would have been even more satisfactory.

